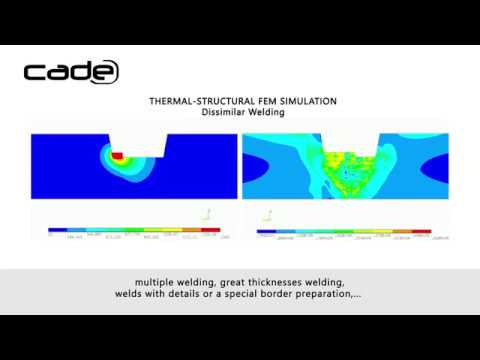
You can see more about structural analysis and engineering simulation on this link:
--------------------
First, it is conducted a transient-state thermal simulation in which welding passes are characterized. Such characterization is based on those parameters defined in the Welding Procedure Specification (number of passes, feed rate, thermal heating power, melting temperature...). Additionally to this, phase change of material might also be implemented on the thermal simulation. The analysis allows to determine temperature fields at seam weld, (Heat-Affected zone) and base materials.
After thermal simulation, a transient-state structural analysis is conducted to determine the strain and stress states, during and after the welding process. Through this analysis the contraction strains and residual stresses that welding after cooling might present, are evaluated. This methodology also allows to foresee which areas would be susceptible to develop microcracks, based on the triaxial stress states, developed along the welding process cycle.
The Welding Process Simulation is a very useful methodology, particularly helpful for dissimilar welding, multiple welding, great thicknesses welding, welds with details or a special border preparation, etc. Welds on which a right definition of its specific welding procedure is the key for a successful result.
0 Comments